Our CMRP-certified professionals with over 10 years of experience provide comprehensive plans to enhance equipment reliability, reduce downtime, and optimize maintenance costs.
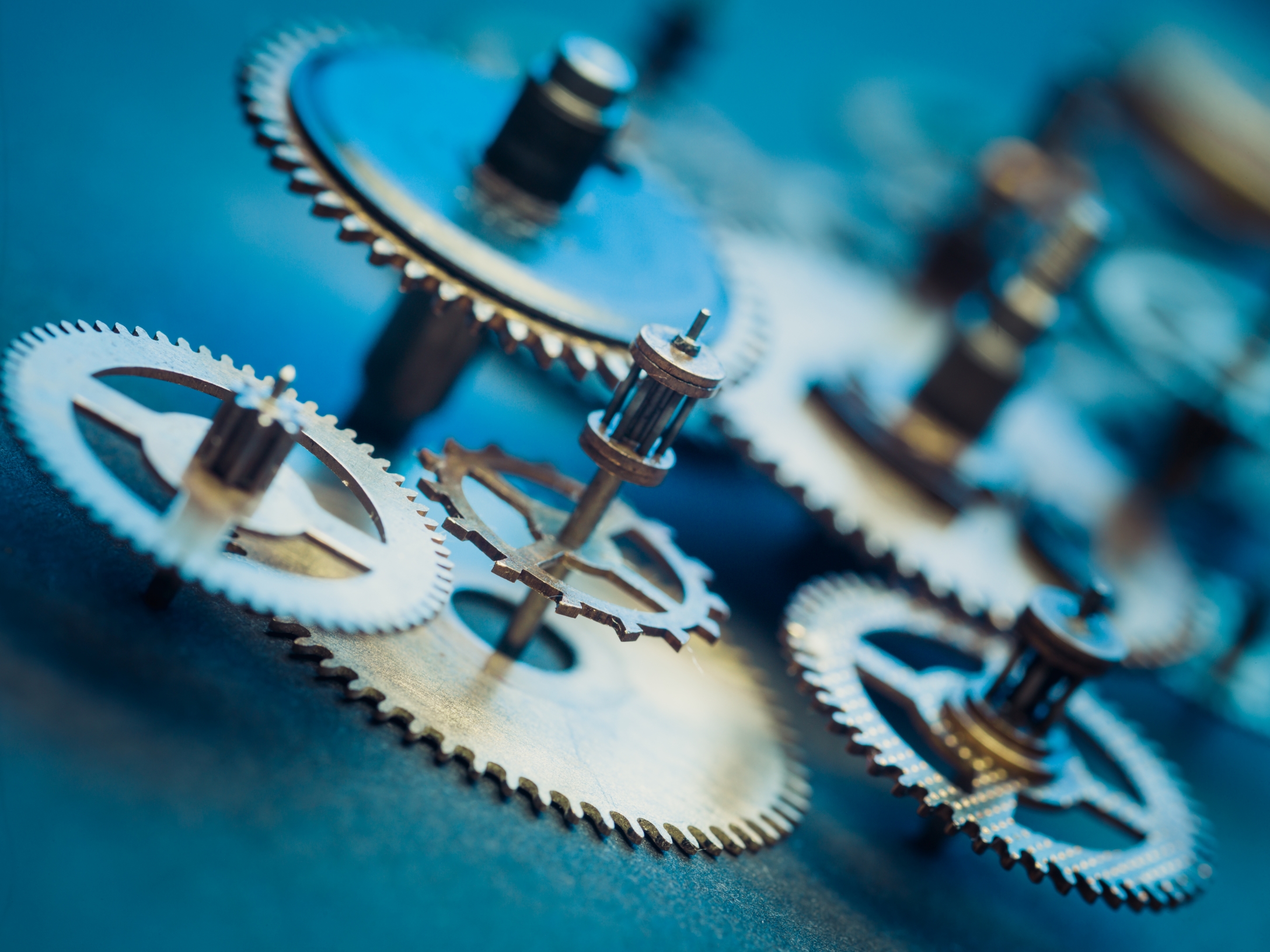
Maintenance and Reliability Strategy Implementation Plan
Our maintenance and reliability professional are CMRP certified and comes with more than 10 years’ experience in Manufacturing, oil and gas , and Mining . We offer Ma comprehensive maintenance and Reliability Strategy Implementation Plan is a 3 comprehensive document that outlines the steps and actions required to effectively implement a maintenance and reliability strategy within an organization. Here's a breakdown of what such a plan typically involves: Objectives and Goals: Define the objectives and goals of the maintenance and reliability strategy implementation plan. These may include improving equipment reliability, reducing downtime, extending asset lifespan, optimizing maintenance costs, and enhancing overall operational efficiency. Current State Assessment: Conduct a thorough assessment of the current maintenance and reliability practices, processes, and performance within the organization. Identify strengths, weaknesses, opportunities, and threats related to maintenance and reliability.
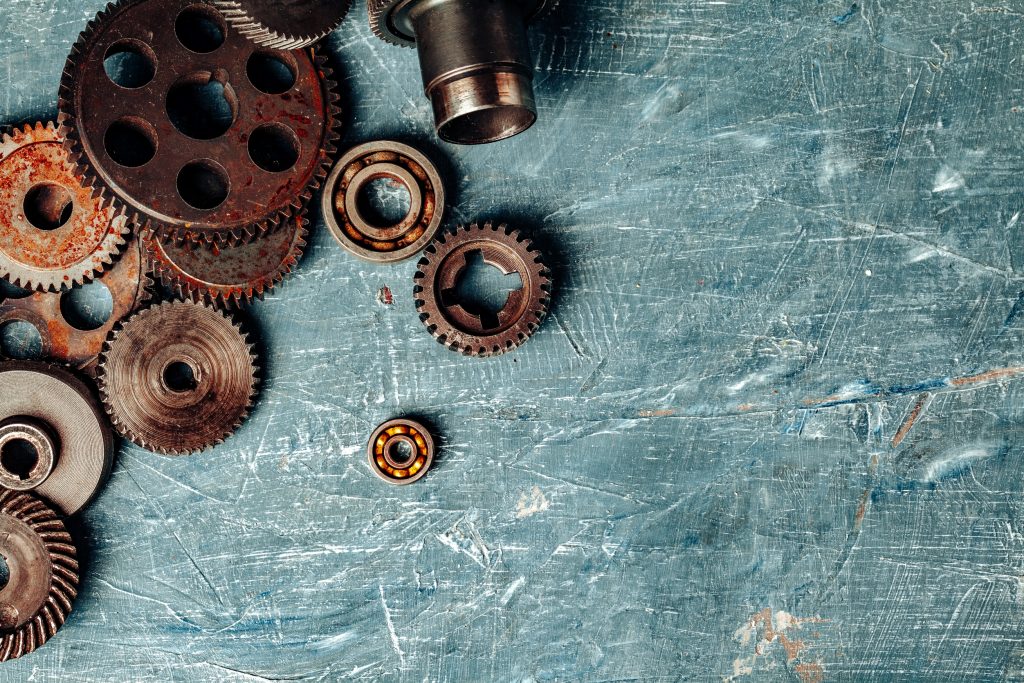
Maintenance and Reliability
Maintenance refers to the activities and practices undertaken to keep equipment, machinery, or infrastructure in a functional and operational state. It includes preventive maintenance (scheduled inspections and tasks to prevent breakdowns), predictive maintenance (using data to predict when maintenance is needed), and corrective maintenance (repairing or replacing components after a breakdown).
- Minimize Downtime
- Optimize Efficiency
- Extend Lifespan
- Expert Analysis
- Enhance Safety
Steps
Develop a tailored maintenance and reliability strategy
based on the organization’s objectives, industry best practices, and the findings of the
current state assessment. This strategy should encompass various aspects, including
preventive maintenance, predictive maintenance, reliability-centered maintenance
(RCM), condition-based maintenance (CBM), spare parts management, and asset
management.
Determine the resources (e.g., personnel, budget,
technology, tools) required to implement the maintenance and reliability strategy
effectively. Allocate resources based on priority areas and projected needs.
Develop a detailed plan outlining the specific actions,
initiatives, and timelines for implementing the maintenance and reliability strategy.
This plan should include milestones, responsibilities, deliverables, and key
performance indicators (KPIs) to measure progress and success.
Identify training needs and develop training
programs to equip personnel with the knowledge, skills, and competencies required
to execute the maintenance and reliability strategy effectively. This may include
training in equipment diagnostics, predictive maintenance technologies, reliability
engineering, and maintenance management systems.
Evaluate and select appropriate technologies and tools to
support the implementation of the maintenance and reliability strategy. This may
include computerized maintenance management systems (CMMS), predictive
maintenance software, condition monitoring equipment, and reliability analysis
tools.
Develop a change management plan to facilitate the
adoption of new maintenance and reliability practices and processes. Communicate
the benefits of the strategy, address concerns, and engage stakeholders at all levels of
the organization.
FAQ
Preventive maintenance involves scheduled inspections, routine tasks (like lubrication and cleaning), and component replacements to prevent equipment breakdowns and ensure ongoing reliability. It is based on calendar or usage-based schedules.
Predictive maintenance, on the other hand, uses data analytics and monitoring technologies (such as vibration analysis or infrared thermography) to predict equipment failure before it occurs. It aims to perform maintenance only when necessary, maximizing uptime and reducing unnecessary maintenance costs.
Reliability is crucial because it ensures that equipment and machinery perform consistently and predictably without unexpected failures. It enhances operational efficiency by minimizing downtime, optimizing production schedules, and reducing repair costs. Reliable equipment also improves safety and ensures consistent product quality, contributing to overall business success and customer satisfaction.
Businesses can improve maintenance practices by implementing a structured maintenance strategy that combines preventive, predictive, and reliability-centered maintenance approaches.
Investing in advanced monitoring technologies and data analytics tools allows for real-time condition monitoring and predictive maintenance scheduling.
Training and empowering maintenance teams with the skills and knowledge needed to perform effective inspections, diagnostics, and repairs.
Regularly reviewing and updating maintenance procedures based on equipment performance data and industry best practices to continuously improve reliability and optimize operational outcomes.